实木板材的缺陷识别与优选排样虚拟仿真实验是科研反哺教学的成功案例,该实验极大地丰富了《自动化综合课程设计》课程内涵。实验总体框架设计包括认知模块、木材缺陷定位、木材缺陷分类和优选排样4大环节,需要2个学时,旨在按照虚实结合的原则,采用激励探究式、任务驱动式等教学方式,使学生通过参加虚拟仿真实验,提升对实木板材缺陷智能识别与优选排样的设计能力、解决复杂工程问题能力,为培养面向现代农林装备及自动化的复合型创新人才发挥积极作用。
本课程为适应实木板材智能制造业高质量发展的需求,以培养具有解决复杂工程问题能力和创新思维能力的高层次人才为目标,坚持“学生为中心、产出导向、持续改进”的原则,以实木板材的缺陷识别与优选排样为切入点,有效地解决现实实验开展中存在的难点:
1、高危险性:实木板材生产过程中粉尘多、噪声大,高速切割设备锯切速度高(每秒锯切5-8次,且木材易飞出伤人),实验危险性大,开展实体实验的防护要求高。
2、大型综合实验:目前实木板材的缺陷识别与智能制造系统采用大型自动化生产线,生产设备体积大,实验场地受限,导致大规模生产设备不能在实验室再现,对应的实体实验环节多,实验复杂,属于大型综合实验。
3、不可逆性:、设计参数耦合度高,智能算法复杂,实验难度大,获得实验结果的实效性差,易导致出现木材误切的不可逆操作。我国属于典型的少林国家,实木板材资源十分匮乏,如果学生设计的算法效果不佳更易造成实木板材的浪费。
实验课程瞄准培养学生解决复杂工程问题的能力,采用多层次结构,从缺陷定位、缺陷分类到优选排样,层层递进,兼具知识的深度与广度,充分利用最新的虚拟仿真技术的高仿真特性、交互特性,从对工业机器人、电机、加工设备、实木板材缺陷等基础认知到图像预处理、神经网络和遗传算法优选的高阶仿真,各实验环境的设计与实施都侧重于培养学生的自主探究、学习能力,使其熟悉工业现场环境,提高对板材缺陷识别与优选排样的设计能力、创新开发能力及独立解决问题能力。
①教学理念的先进性。实验坚持以学生为中心的教学理念,将立德树人和思政教育融入教学过程,采用任务驱动式、激励探究式、自主学习式等多种教学模式提高学生学习兴趣。虚拟仿真实验将林业生产与人工智能技术深度融合,将原先被废弃的板材短料切除缺陷后接长排样再利用,变废为宝,最大限度地利用木材,提高了木材资源的利用率,响应了“绿水青山就是金山银山”的发展理念,贯彻了减少木材消耗就是植树造林的思想。
②实验内容具有高阶性。本虚拟仿真实验课程是科研成果反哺教学的案例,项目团队自主研发的实木板材智能化识别生产加工核心技术已经达到了行业内领先水平,实验内容涉及多学科领域知识交叉融合,利用项目式教学充分培养学生的工程素养、解决复杂工程问题的能力和高阶思维。
③实验设计具有挑战度和创新性。实验教学模块源于木材加工智能装备龙头企业的实际工程应用案例,符合当今国家对传统企业进行转型升级的要求。在实验中设置了很多设计参数,算法复杂,交由学生自主探索,学生需要在实验报告中对比分析实验结果,提升多途径、多方案的自主创新设计能力,并对出现的问题原因及改进措施深入分析,着重考核学生解决复杂工程问题的能力,在实验设计上难度逐步提升,通过“理解——设计——优化”的知识层次递进,不断激发学生的创新思维。
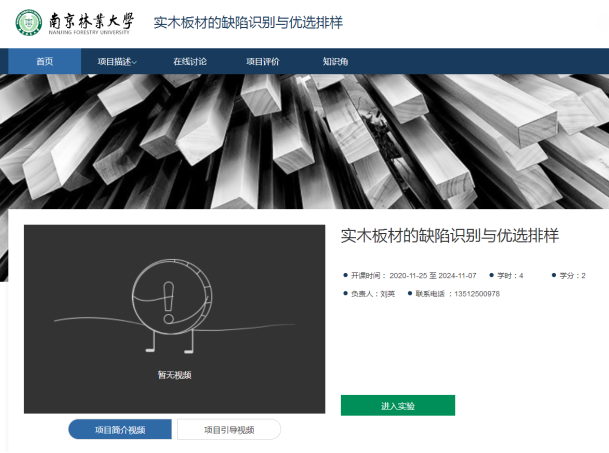
图1虚拟仿真实验主页面
2开始实验
学生进入“实木板材的缺陷识别与优选排样虚拟仿真实验”,进入主页面,选择“进入实验”,进入实木板材的缺陷识别与优选排样虚拟仿真实验场景欢迎界面。

点击确定进入实验场景页面,如图3所示,首先要阅读实验指南和实验简介(图4)点击右上角的“知识角”,会获取与本实验相关的科技前沿、学术文章以及课程知识点。本实验分为三个模块,每一个模块均为激活状态,学生点击任一模块,从而选择相应的实验。
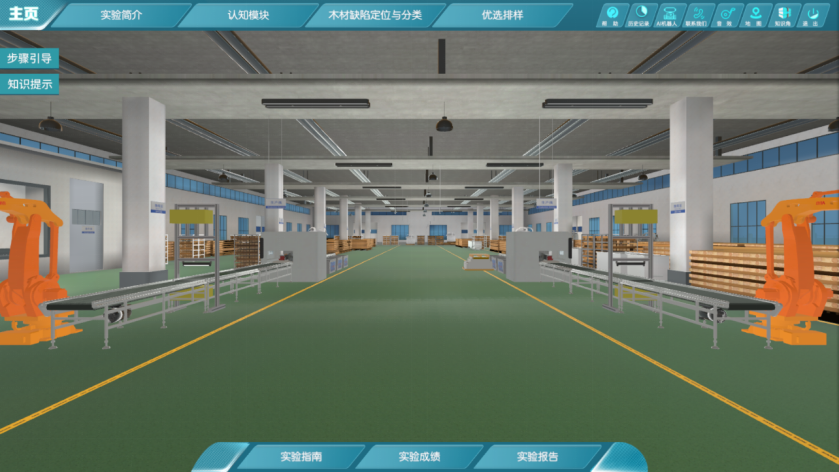
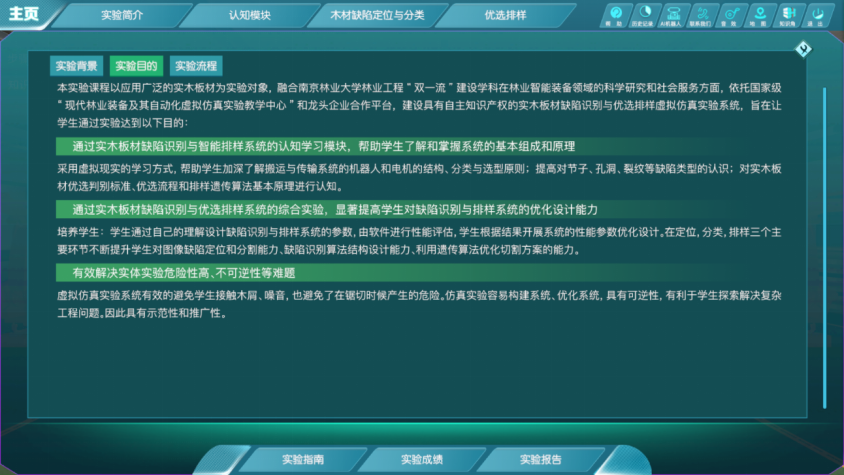
图4实验简介