实木板材的缺陷识别与优选排样虚拟仿真实验
实木板材的缺陷识别与优选排样虚拟仿真实验是科研反哺教学的成功案例,该实验极大地丰富了《自动化综合课程设计》课程内涵。实验总体框架设计包括认知模块、木材缺陷定位、木材缺陷分类和优选排样4大环节,需要2个学时,旨在按照虚实结合的原则,采用激励探究式、任务驱动式等教学方式,使学生通过参加虚拟仿真实验,提升对实木板材缺陷智能识别与优选排样的设计能力、解决复杂工程问题能力,为培养面向现代农林装备及自动化的复合型创新人才发挥积极作用。
实验步骤
1开始试验
1 学生进入“实木板材的缺陷识别与优选排样虚拟仿真实验”,进入主页面,选择“进入实验”,进入实木板材的缺陷识别与优选排样虚拟仿真实验场景欢迎界面如图2。
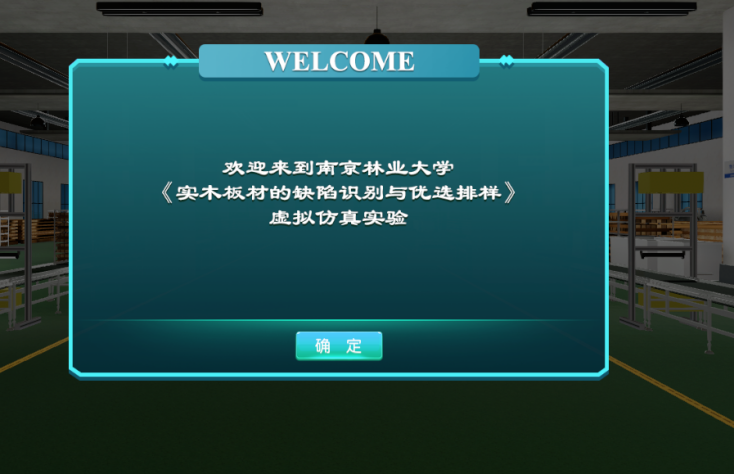
2 点击确定进入实验场景页面,如图3所示,首先要阅读实验指南和实验简介(图4)点击右上角的“知识角”,会获取与本实验相关的科技前沿、学术文章以及课程知识点。本实验分为三个模块,每一个模块均为激活状态,学生点击任一模块,从而选择相应的实验。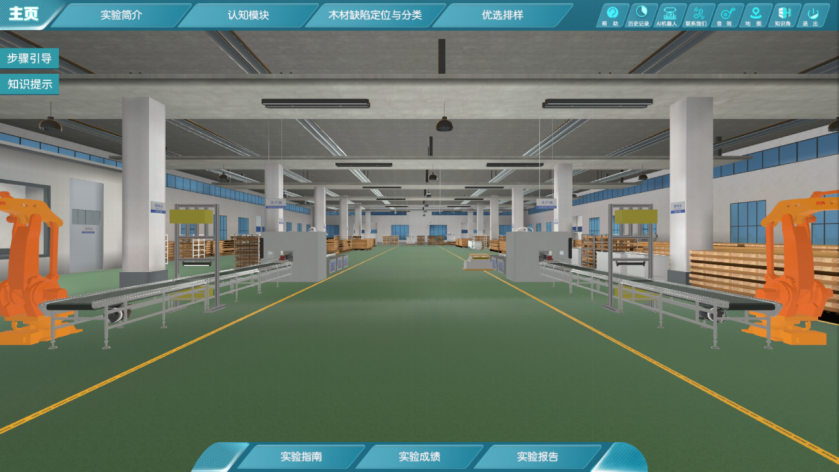
图3 实验漫游场景
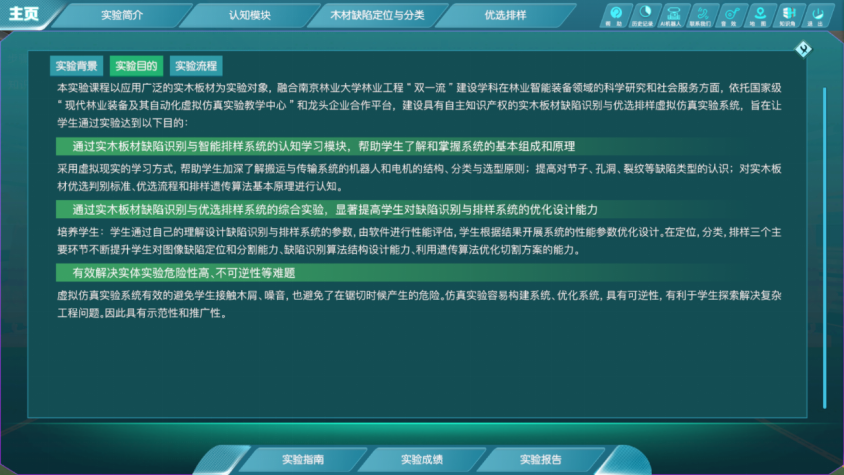
图4实验简介
下面分别介绍“系统认知模块、木材缺陷定位与分类模块、优选排样模块”三个模块的实验模块。
END
模块一:认知模块
1步骤1
在实验选择页面(如图5所示),点击“认知模块”,进入实验系统认知环节。
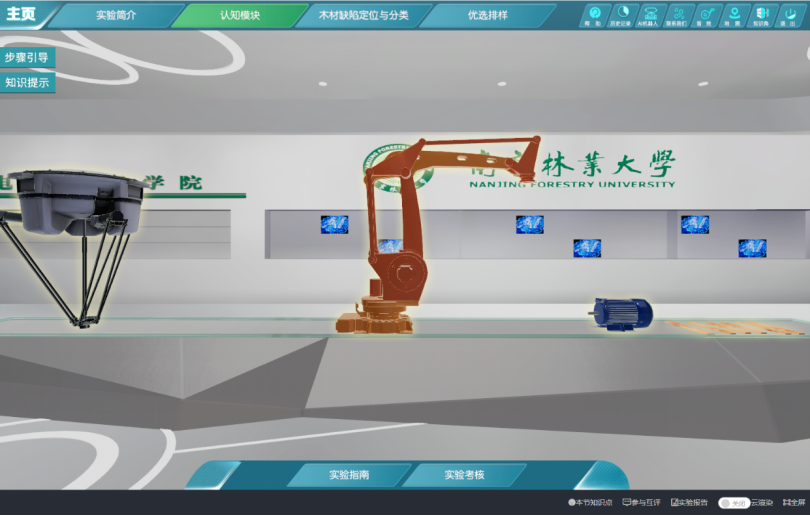
图5系统认知环节主界面
2步骤2
② 点击“机器人”的“机器人介绍”,可以对机器人的类型特点进行认知学习,如图6所示。
图6 机器人认知学习
3步骤3
③点击电机的“电机介绍”、“爆炸显示”,可以观察电机相应实际模型,子界面会出现相应标签说明。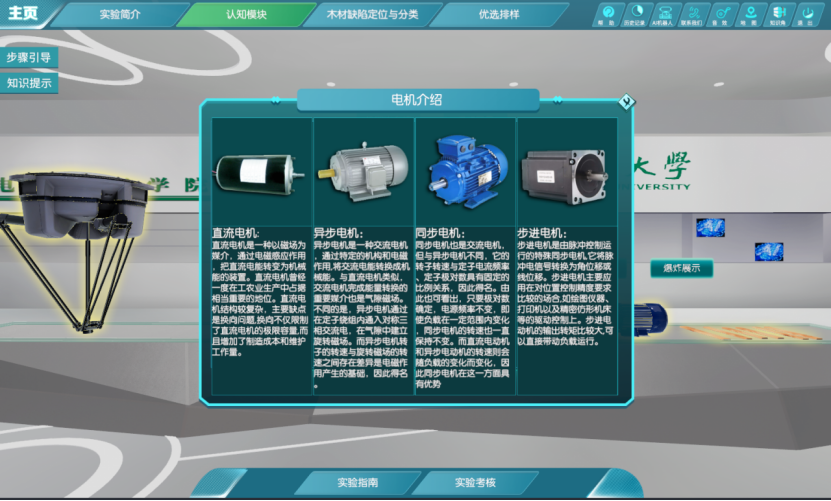
图7 电机类型认知
4步骤4
④电机桌面上的板材,出现常见板材介绍界面,可以对实木板材缺陷类型和优选流程、遗传算法认知学习。
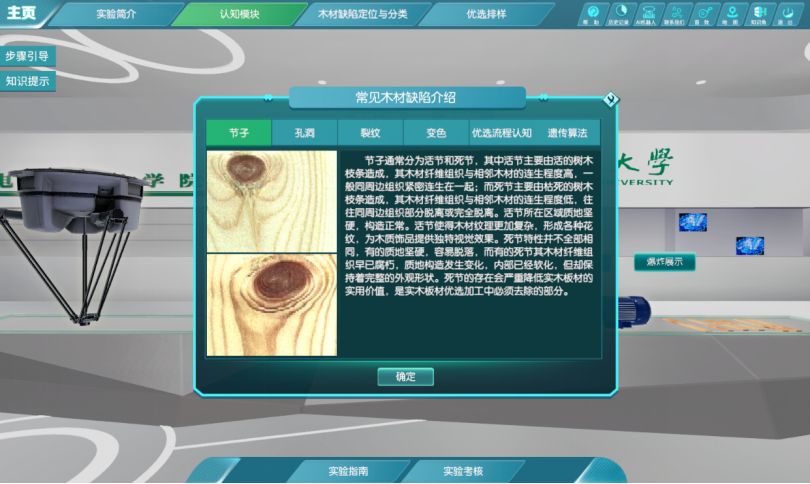
图8 板材缺陷类型认知
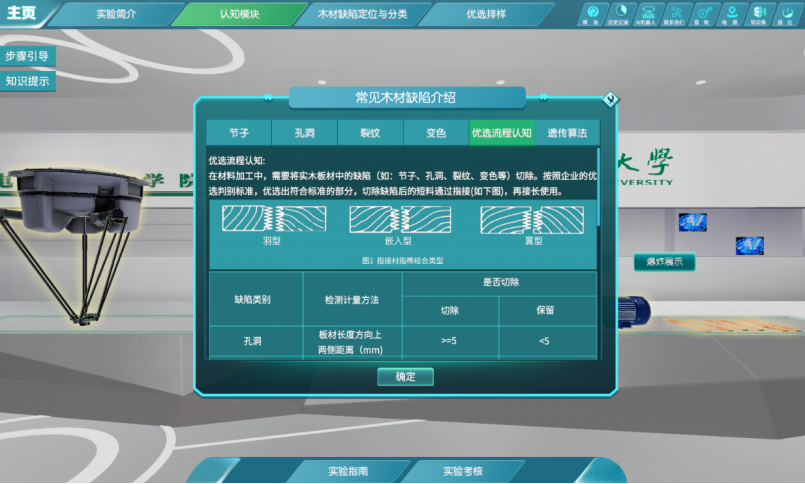
图9 优选流程认知
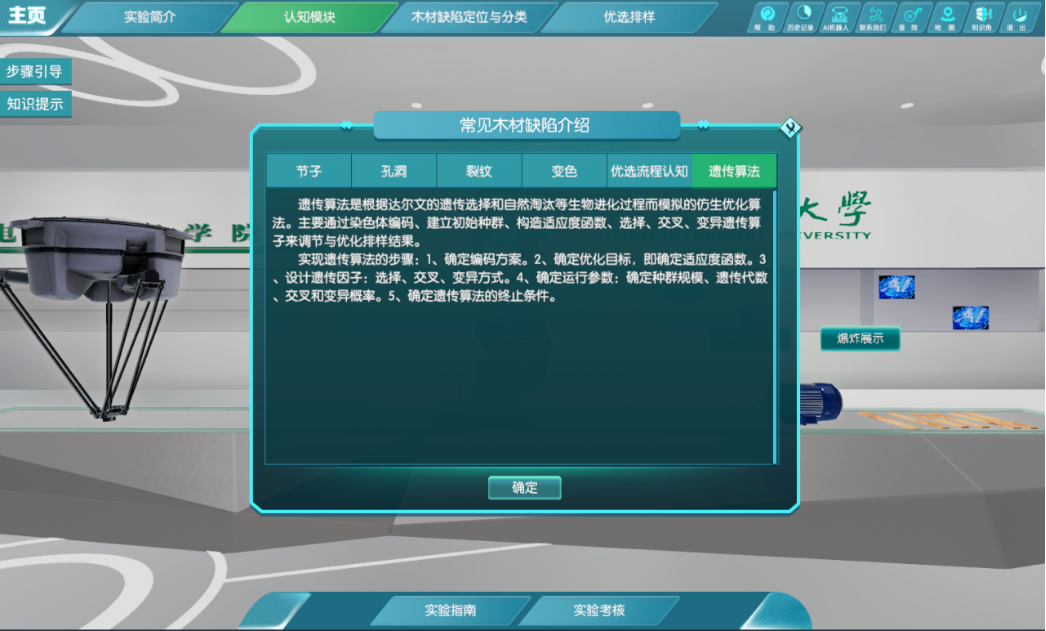
图10 遗传算法知识认知学习
5步骤5
⑤实验考核,点击下方的“实验考核”,完成三个测试题。提交认知成绩。 END
模块二:木材缺陷定位与分类
1步骤1
① 点击“木材缺陷定位与分类”,出现实验任务1(图12),点击“确定” 进入工程机器人搬运木材界面(图13)。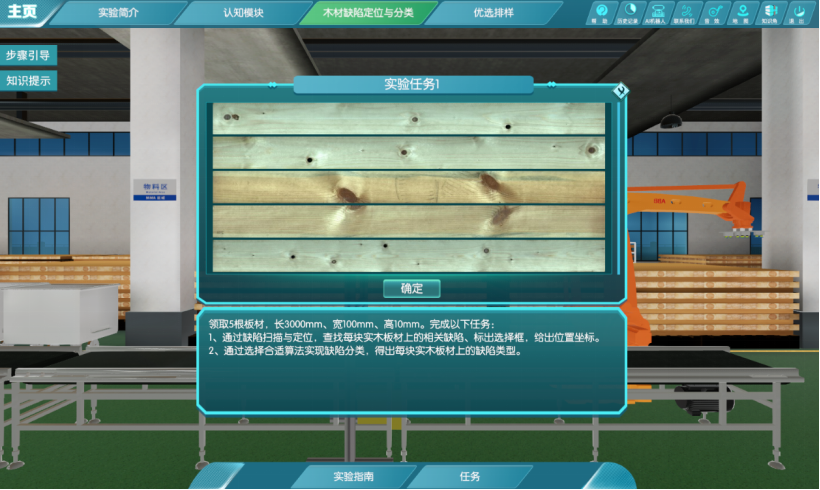
图12领取任务1界面
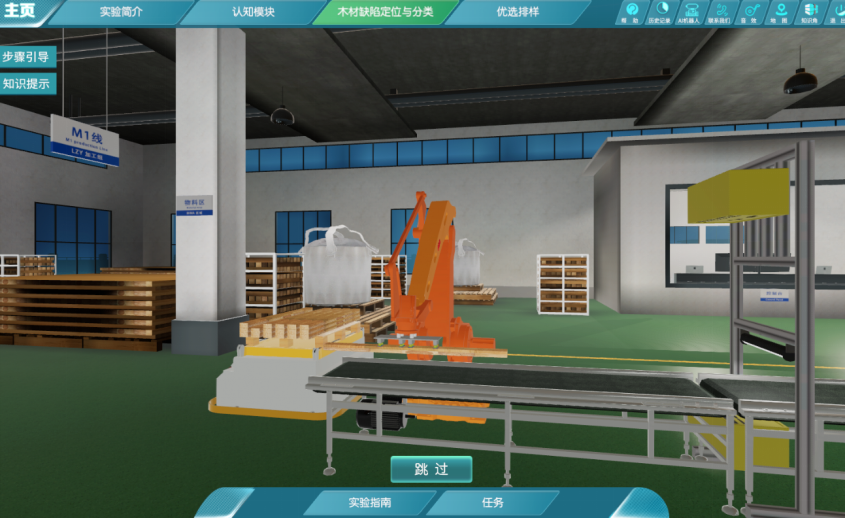
图13 生产场景机器人搬运板材
2步骤2
② 机器人搬运结束或者点击“跳过”按钮,场景切换到控制室(图14),依次点击控制室的高亮电脑,出现定位与分类流程(图15)与扫描界面(图16)。图14 控制室场景
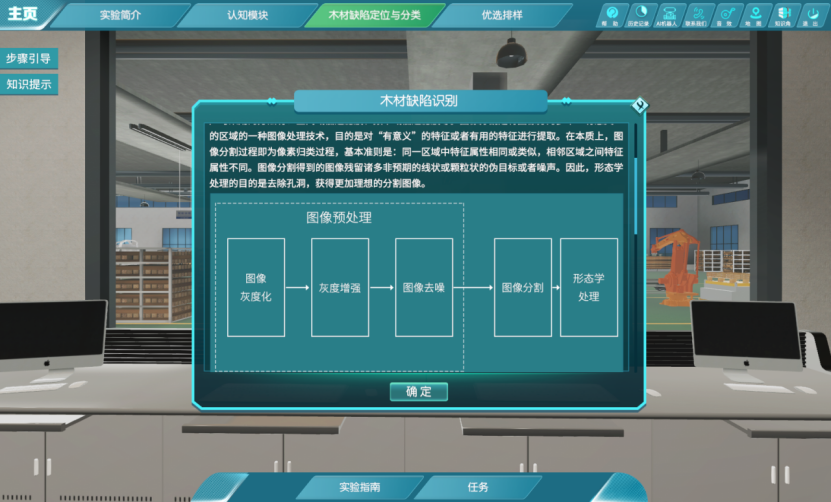
图15缺陷识别流程
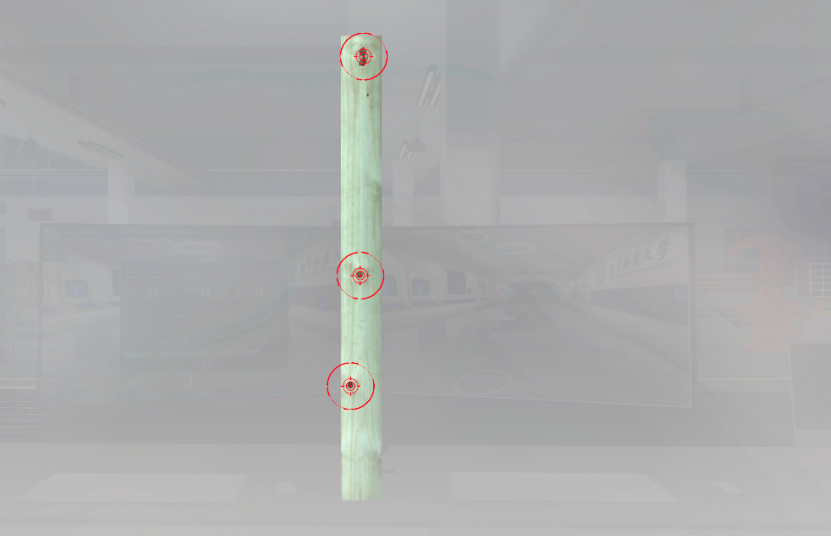
图16扫描仪扫描界面
3步骤3
③ 图像采集完毕,控制室右端出现4个实验子环节。点击右侧阴影部分可以隐藏和显示。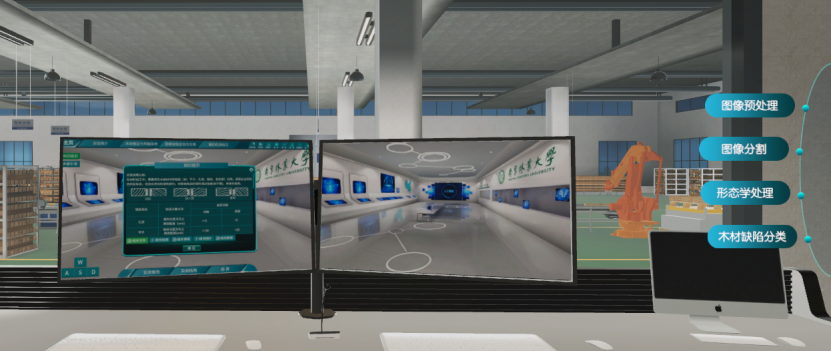
图17图像定位与分类子功能按钮
4步骤4
④ 点击“图像预处理”,在阅读预处理知识点提示后,点击“继续”进入图形预处理界面,输入斜率K和截距C参数,观察变换效果(图18)。还可以通过点击图片上的“绿色问号”了解小提示。
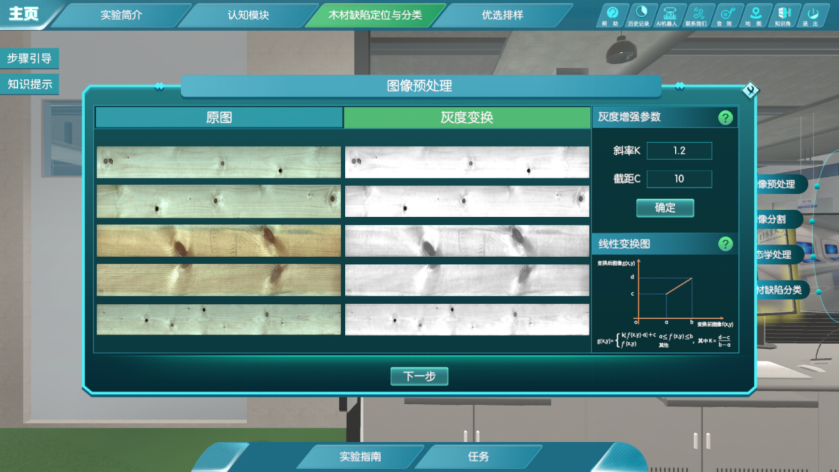
图18 实木板材图像灰度变换结果
5步骤5
⑤ 查看完灰度变换结果后,点击“下一步”,阅读完阈值分割知识提示后点击“继续”进入图像分割功能界面。系统提供两种阈值分割方法,先选择一种方法,通过进度条或者数值输入的方式改变阈值大小,点击“确定”观察阈值分割的效果(图19)。根据参数设置提示(图20)优化分割结果。
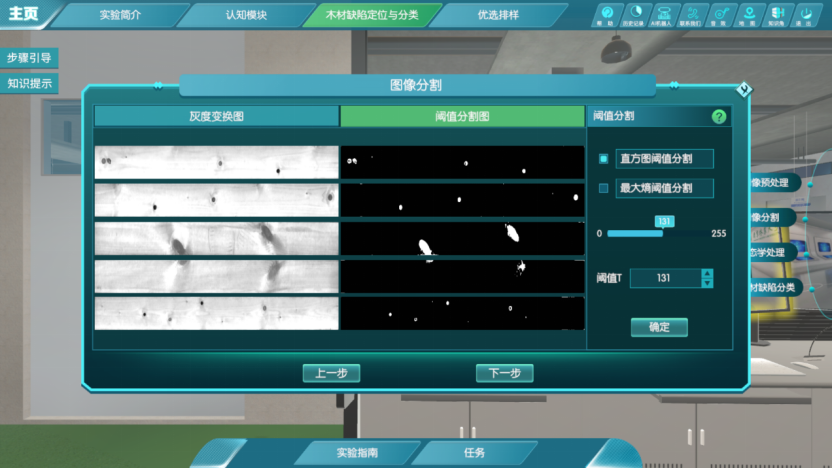
图19 图像分割结果
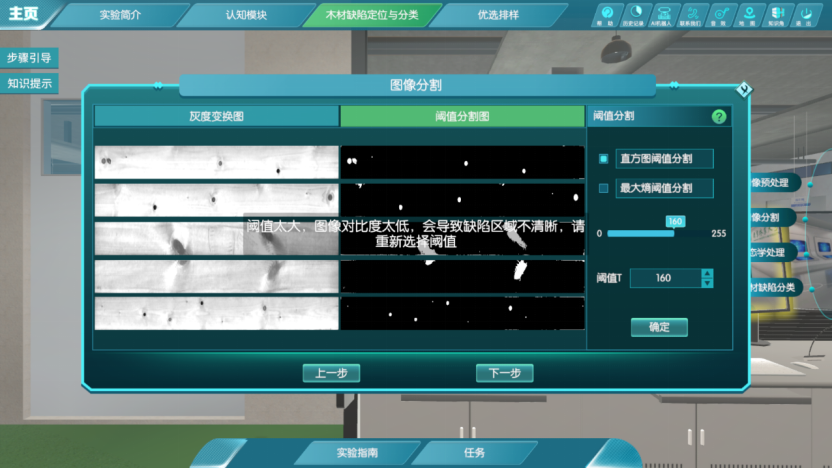
图20阈值设置提示
6步骤6
⑥ 在两种分割方法都完成阈值分割后点击下一步进入阈值分割结果对比分析界面,对比分析后选择其中较为满意结果(如图21)。
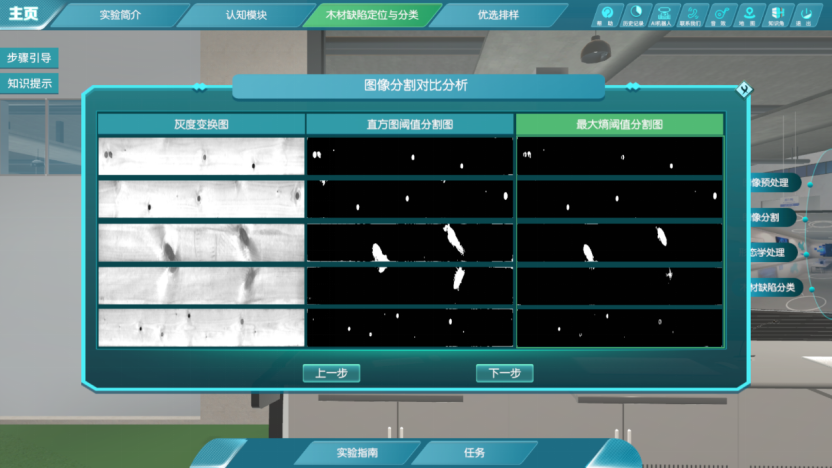
图21阈值分割结果对比选择
7步骤7
⑦ 点击“下一步”,阅读形态学处理知识提示后点击“继续”进入形态学处理界面。在界面上选择结构元素大小、形状,设置对应的腐蚀和膨胀次数。学生点击“确定”观察形态学处理结果(图22),优化参数。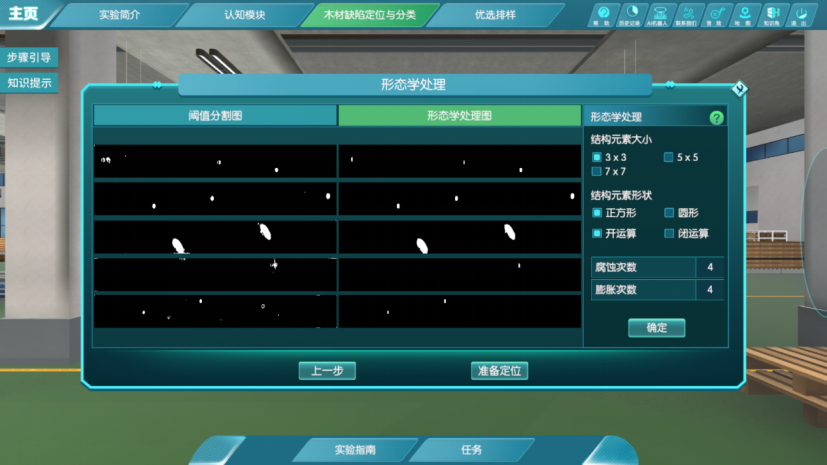
图22 形态学处理结果
8步骤8
⑧点击“准备定位”,进入定位结果显示界面,点击绿色区域观察缺陷所在位置的坐标(图23)。X代表区域的初始位置,△X表示缺陷宽度。
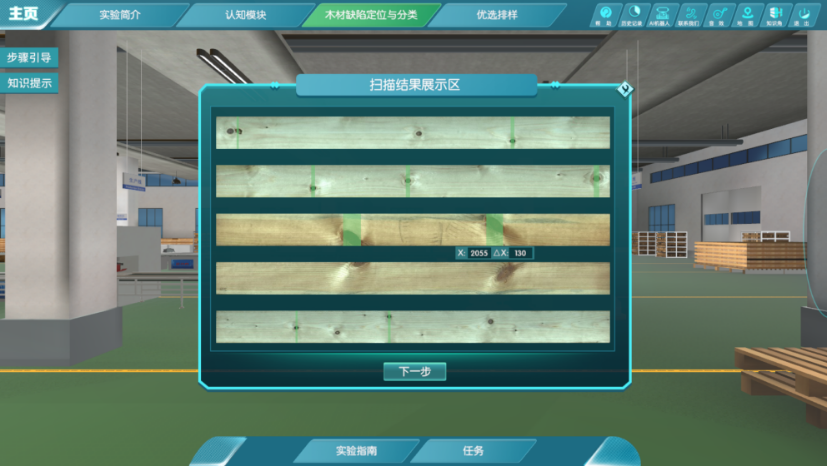
图23 定位结果查看
9步骤9
⑨点击“下一步”,进入缺陷分类算法选择界面(图24)。了解两种算法理论后,选择基础算法,点击“确定”。
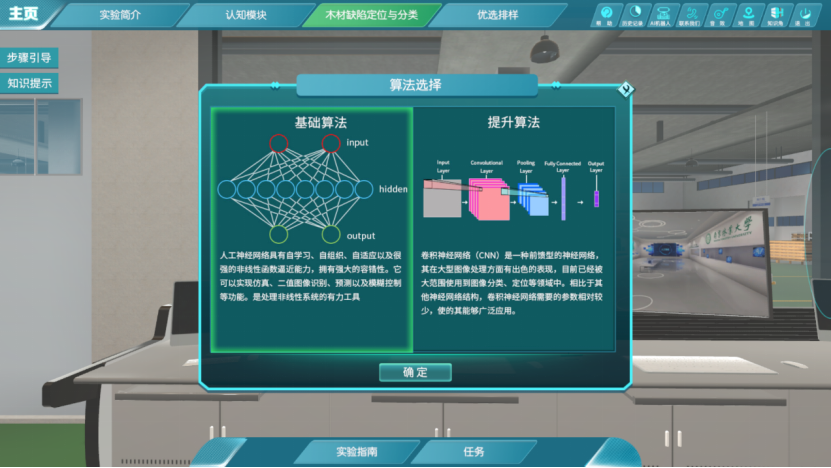
图24 缺陷分类算法选择
10步骤10
⑩点击“确定”,进入基础算法-人工神经网络算法设计界面(图25),通过绿色问号小提示,把知识点再深入了解一下。然后在界面上设计边缘特征、颜色特征和纹理特征,调节输出节点数和中间隐层数,以及各个隐层节点数。
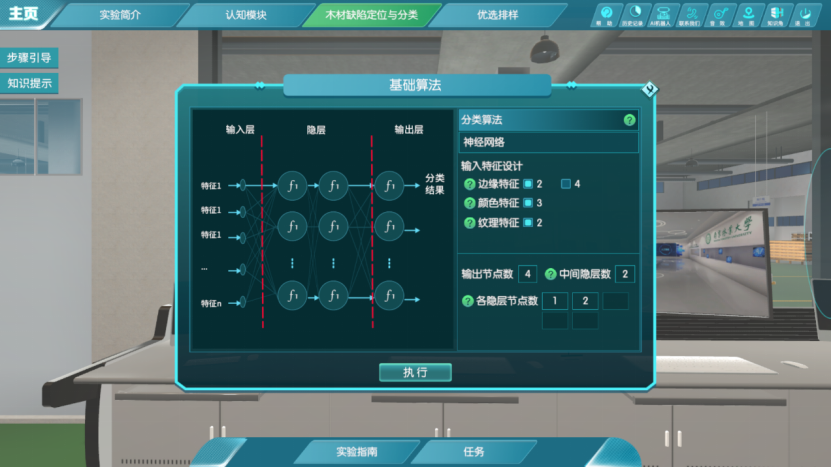
图25 缺陷分类人工神经网络算法设计
11步骤11
⑪点击“执行”,获得缺陷识别分类的结果(图26),观察分类的准确率。点击“查看扫描结果”,查看每根板材的具体缺陷坐标及类型综合信息(图27)。
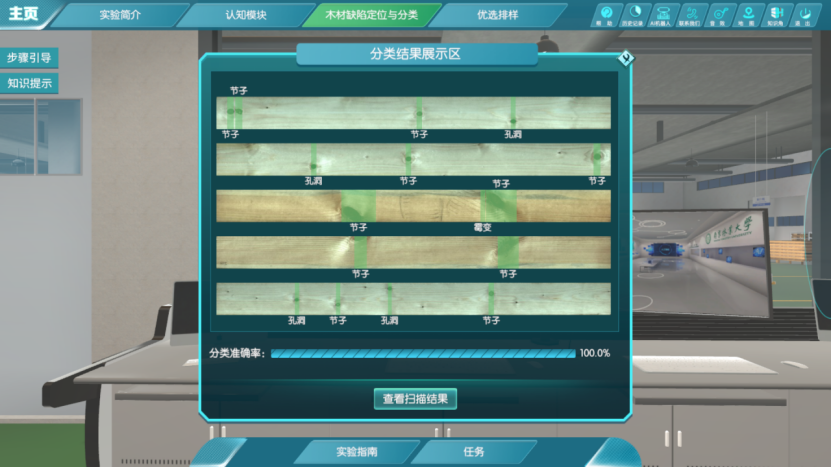
图26 人工神经网络算法分类结果
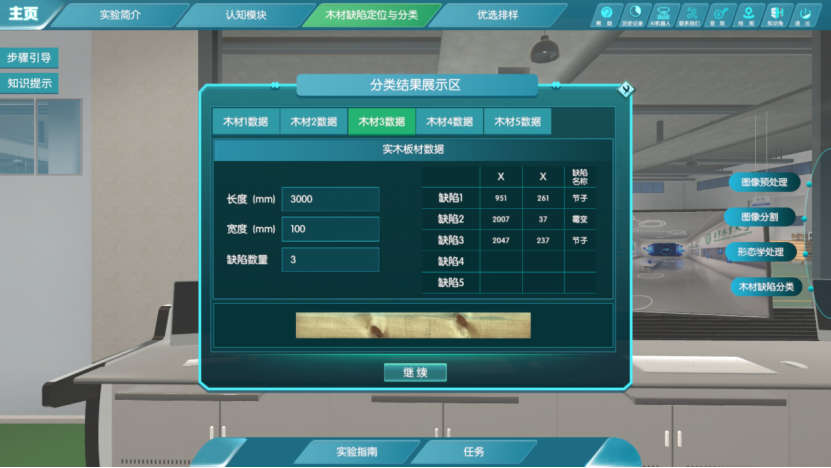
图27每根板材的缺陷位置与类型查看
12步骤12
⑫点击“继续”,出现是否选择提升算法(图28),点击“确定”。进入,卷积神经网络设计界面(图29)。系统提供固定的ABC三种网络结构,学生可以选择,最重要的可以选择自主设计模块,输入卷积网络层数后,自己点击配置卷积层、池化层和正则层及全连接层。
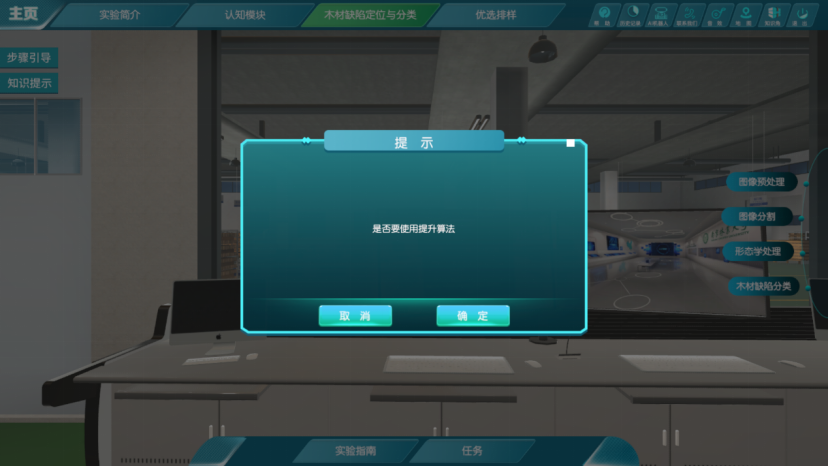
图28 提升算法选择界面
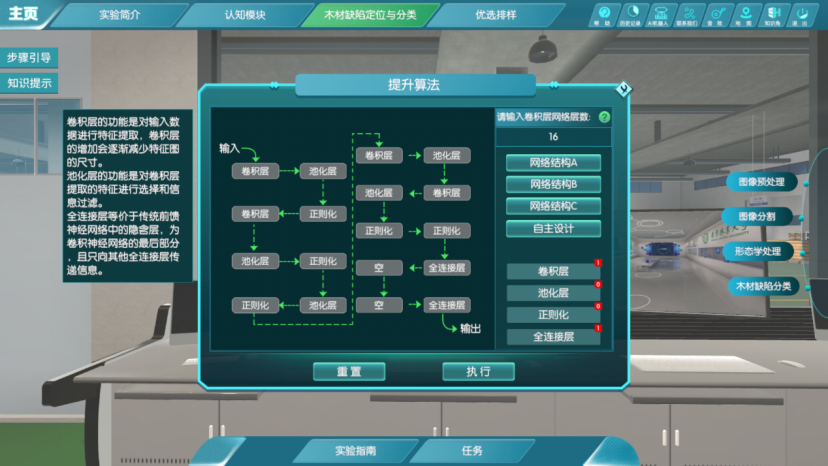
图29 提升算法卷积神网络设计
13步骤13
⑬点击“执行”,观察分类结果和5根板材的具体定位与分类结果。
14步骤14
⑭ 对比分析两种算法结果(图30),可以选择返回定位或者返回分类重新优化实验数据,选择满意结果后点击“确认选择”。结束木材缺陷定位与分类模块的实验。
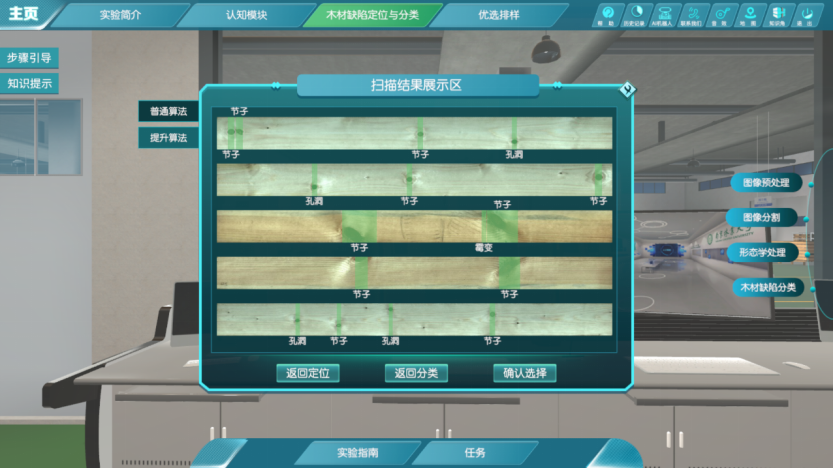
图30普通算法与提升算法对比分析图
END
模块三:优选排样
1步骤1
①点击主界面的“优选排样”,出现实验任务2(图31),根据上一环节的定位与分类结果,分析加工要求。
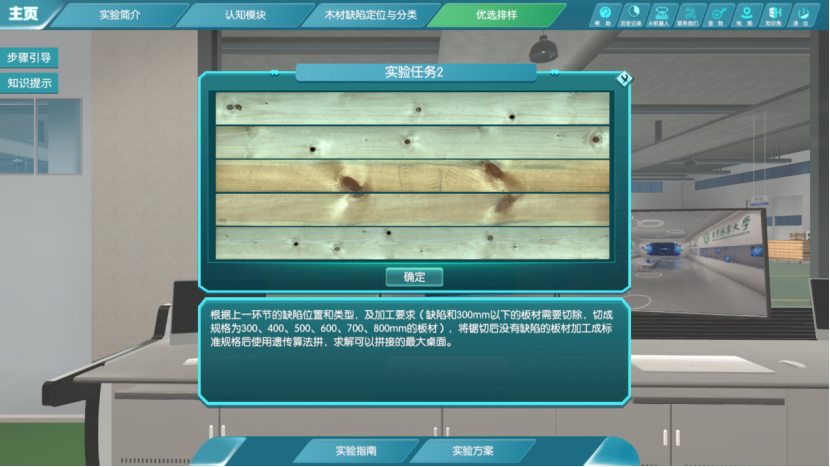
图31 领取实验任务2
2步骤2
②点击“确定”,进入遗传算法设计界(图32)面。左边现实的板材红线是缺陷必须切除的切割线。右边根据加工要求参数规格,设计遗传算法,出材率不一样,对应的新生成蓝线位置不同。在参数输入界面:种群数量参数决定收敛的稳定性,迭代次数参数决定算法是否收敛,交叉概率参数用于判定两个个体是否进行交叉操作,变异概率避免限入局部最优解。
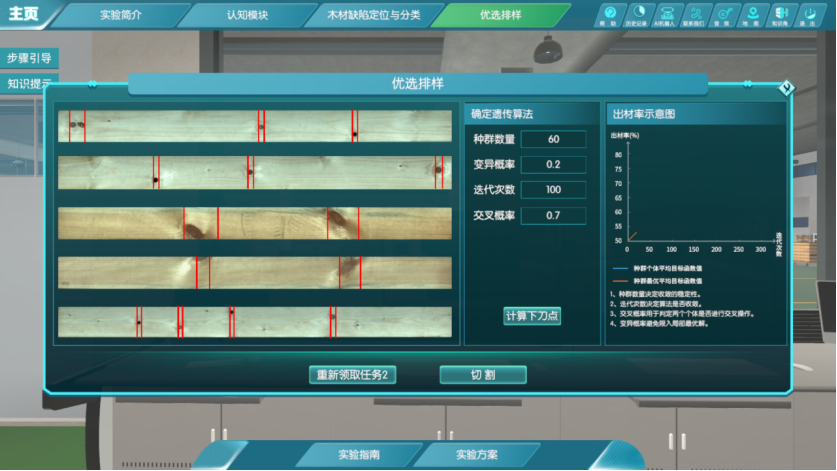
图32遗传算法设计界面
3步骤3
③在其他参数不变的情况下,改变种群数量,计算下刀点,根据结果对比分析种群数量这个参数和出材率之间的关系。(图33)
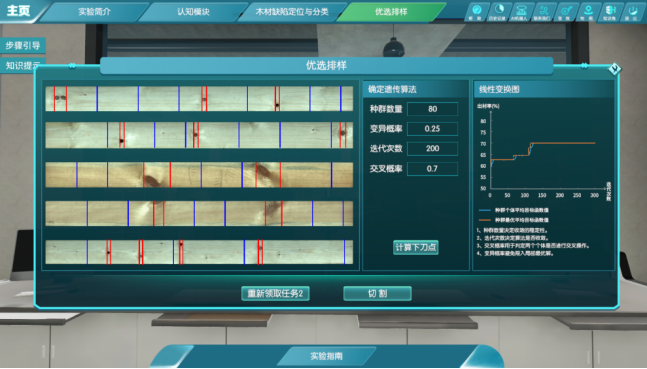
图33 探究遗传算法种群数量与出材率关系
4步骤4
④在其他参数不变的情况下,改变变异概率,计算下刀点,根据结果对比分析变异概率这个参数和出材率之间的关系(图34)。
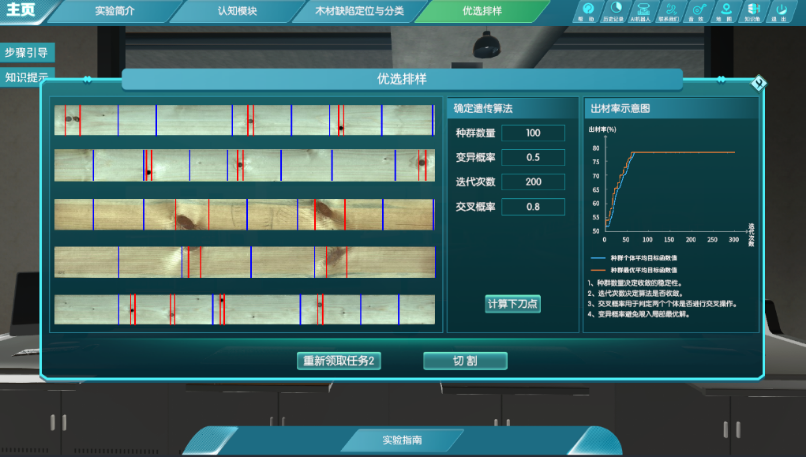
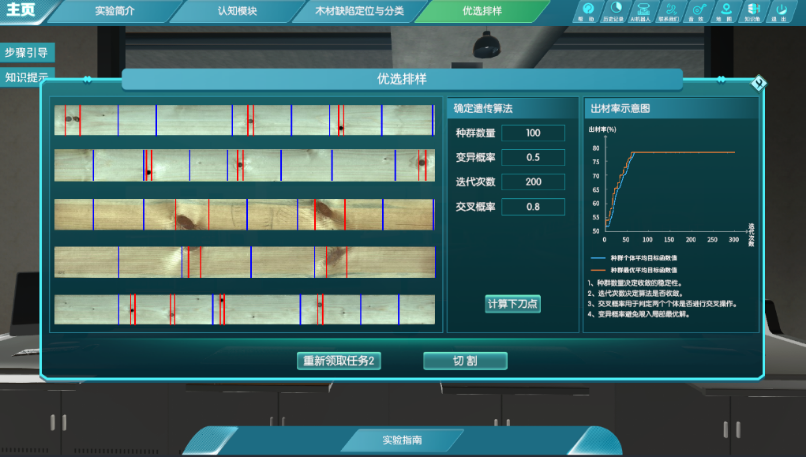
图34变异概率与出材率关系
5步骤6
⑤在其他参数不变的情况下,改变迭代次数计算下刀点,,根据结果对比分析迭代次数这个参数和出材率之间的关系(图35)。
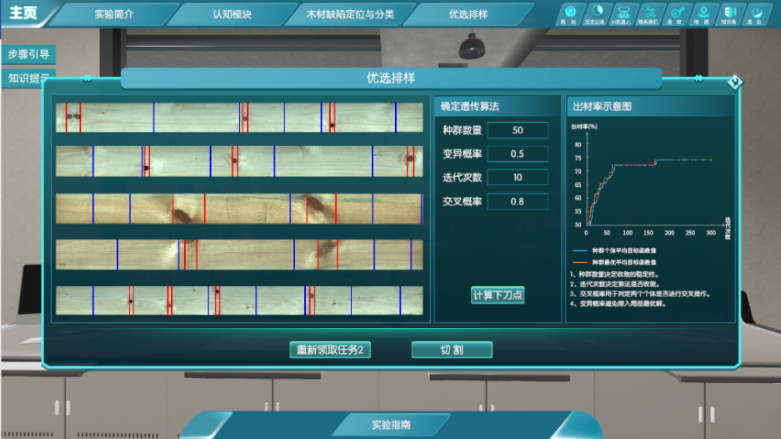
图35迭代次数与出材率关系
6步骤6
⑥在其他参数不变的情况下,改变交叉概率,计算下刀点,根据结果对比分析交叉概率这个参数和出材率之间的关系。
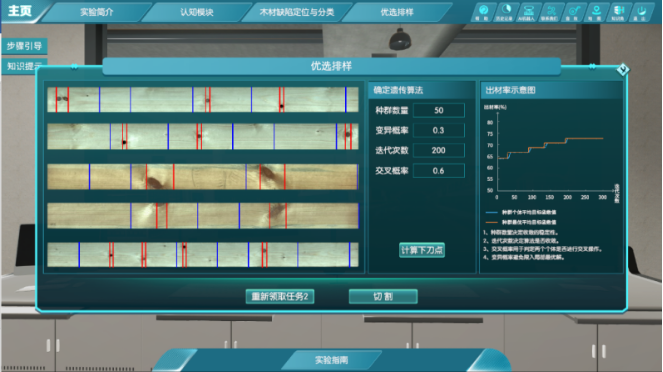
图36 交叉概率与出材率关系
7步骤7
⑦多参数联合调试,探索多参数耦合对算法结果的影响,在上述四个步骤得到各参数合理范围内,适度调整各参数的大小,观测出材率的变化,感知四个参数的耦合度。种群数量太小容易局部收敛,不能得到全局最优或近优解,种群太大又会导致计算时间太长;迭代次数太小会导致还未找到最优解或近优解便停止寻优,太大又会在某个时间节点后材料利用率的提升缓慢的现象,浪费运算时间;变异和交叉概率越大,则算法搜索时的混乱程度越大,越容易达到最优解或近优解,反之则相反。
8步骤8
⑧根据出材率最优解,得出最佳下刀点。点击“切割”,切割机根据下刀点切割木材(图37),即获得无缺陷且符合加工规格的木材,如图38所示。
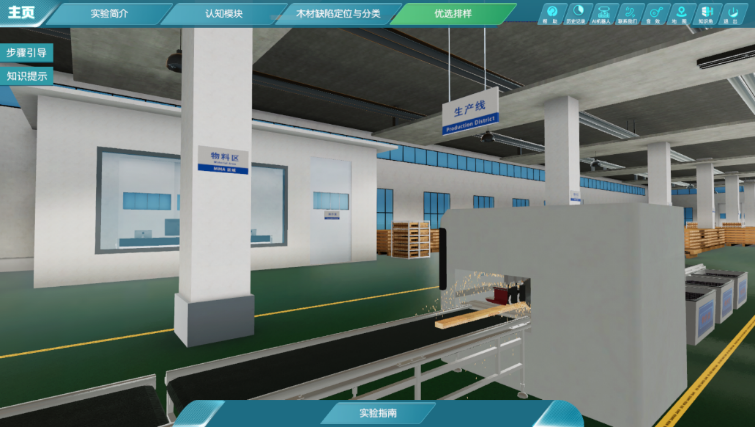
图37 板材切割过程
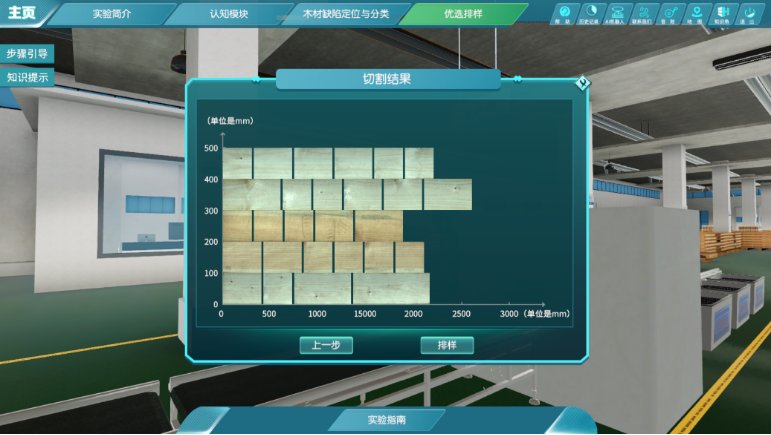
图38 切割结果
9步骤9
⑨点击“排样”,通过前述探究得到合理参数,系统自动得到最优或近优排样结果,并显示排样结果,最终拼接得出最大尺寸的桌面。如图39所示。
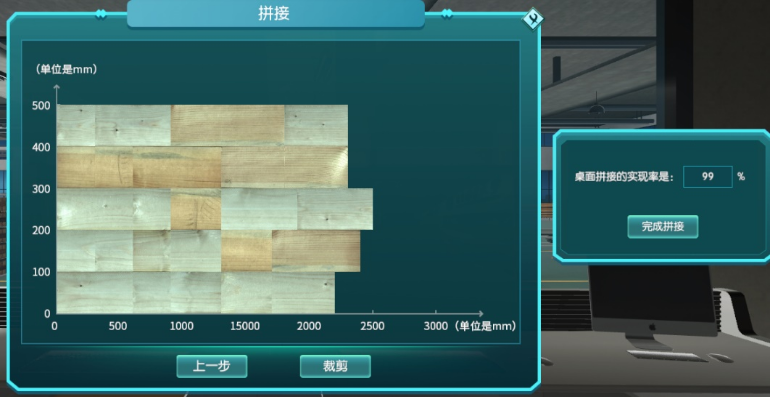
图39 排样结果
10步骤10
⑩点击“裁剪”根据排样结果,获取最大桌面,桌面尺寸和桌面实现率都可见(图40)。
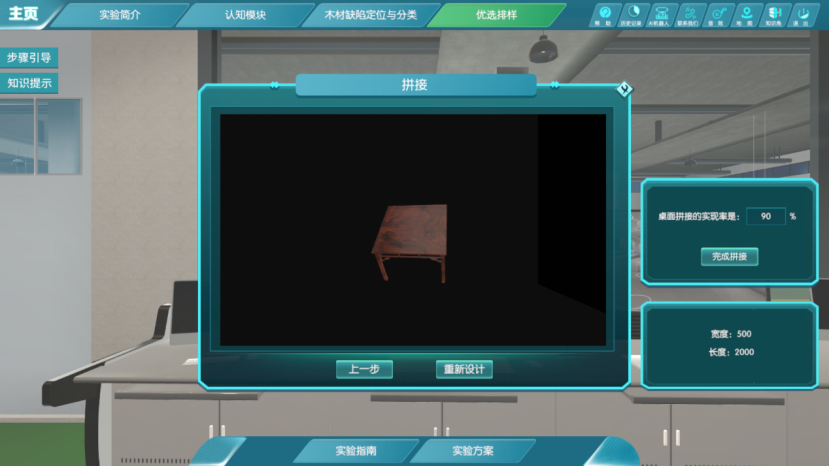
图40 最大桌面拼接成品
11步骤11
⑪满意后可以点击“完成拼接”,如果学生想继续优化结果可以选择“重新设计”。
12步骤12
⑫点击“完成拼接”后,在界面下面点击“实验方案”,观察多次实验结果(图41),查看设计详情。对比分析后选择提交方案。
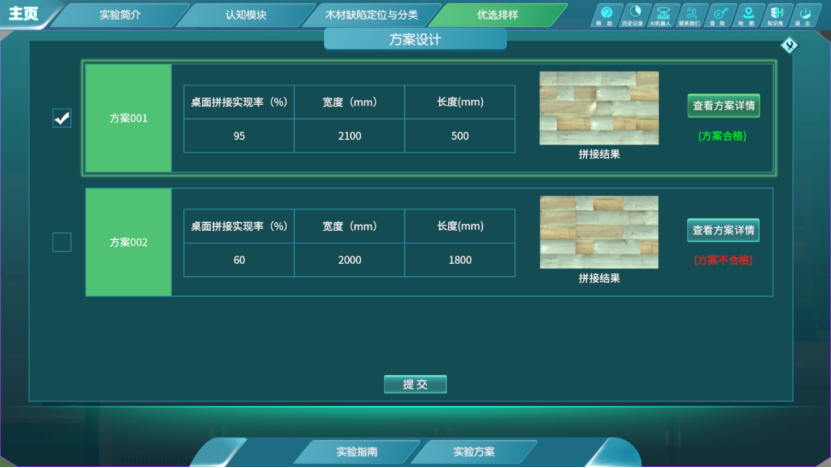
图41多次设计方案对比分析界面
13步骤13
⑬返回主页,点击“实验报告”,查看并完成实验报告的相应部分(图42)点击“提交”完成实验。
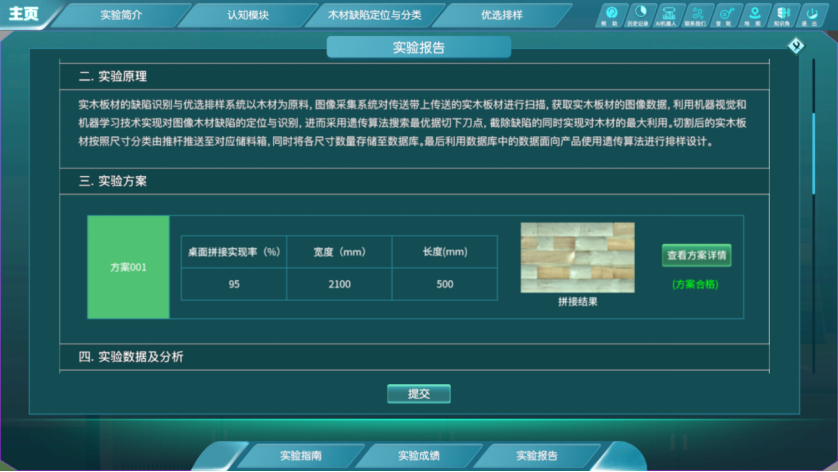
图42实验报告
END